Transport. Fleet. Billing. Fretron powers every logistics layer—customized to your unique processes, backed by domain expertise and designed to drive efficiency and cost savings!
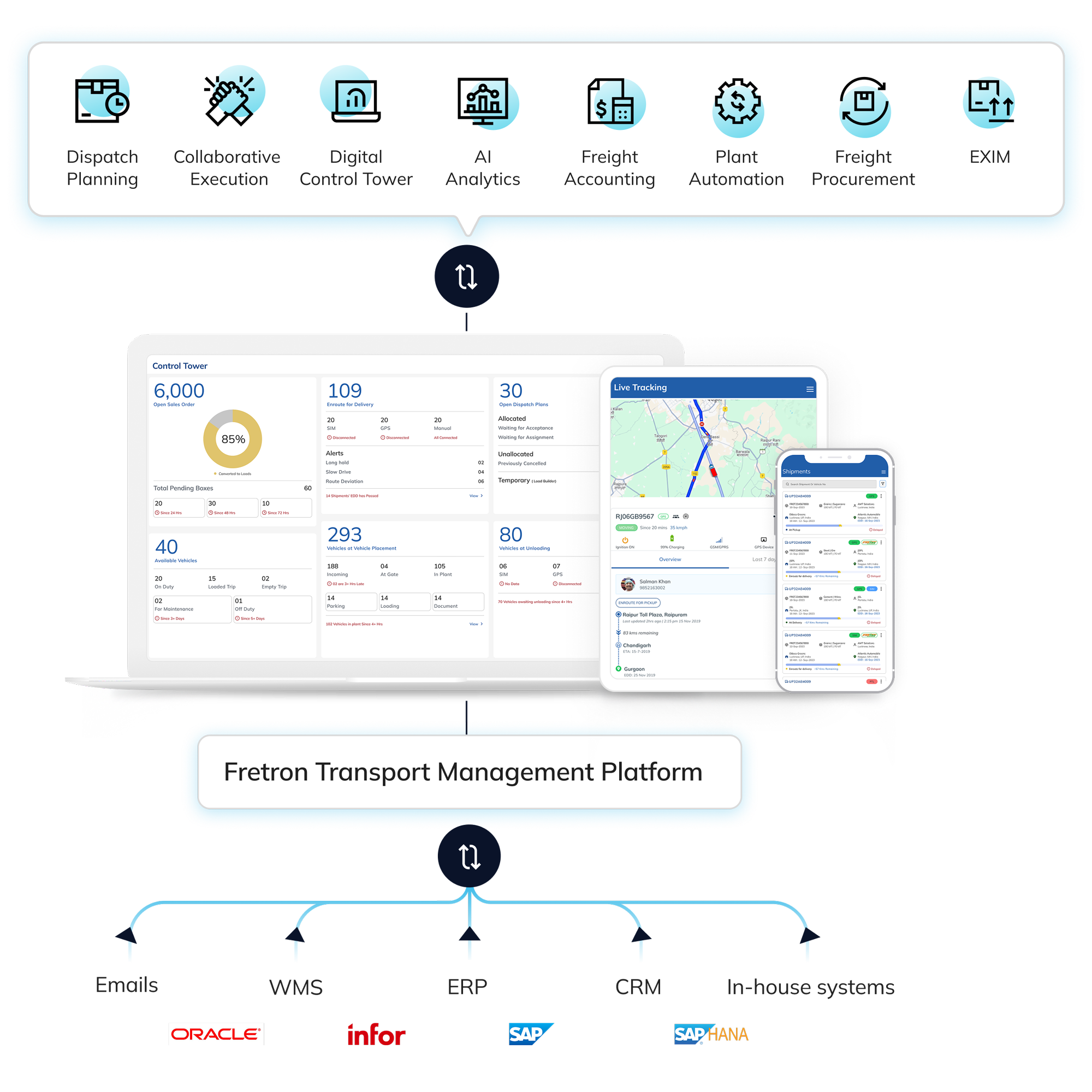
Leading supply chain teams #MoveAsOne with Fretron
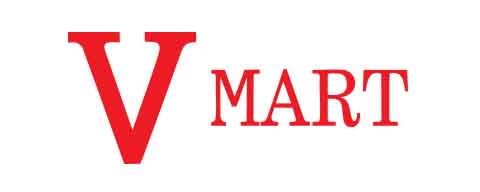
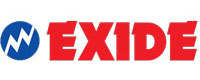
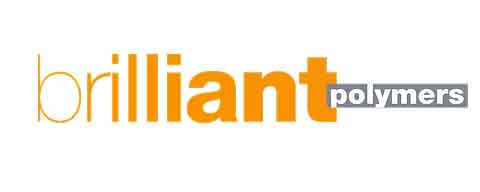
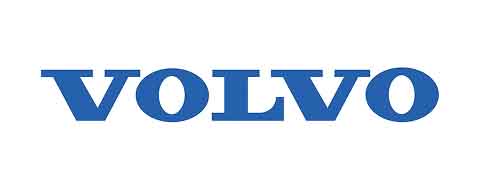
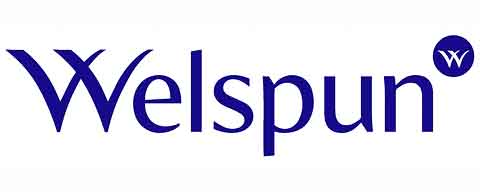
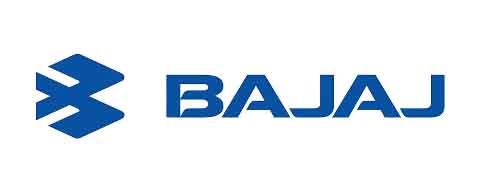
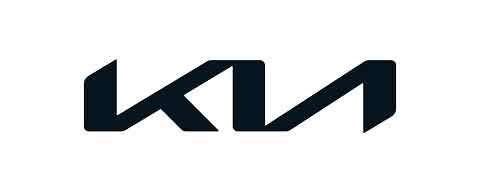
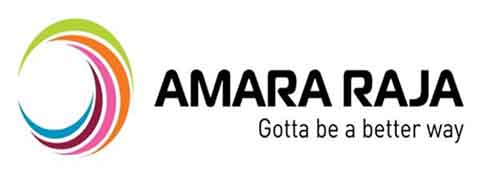
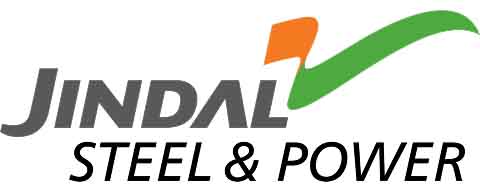
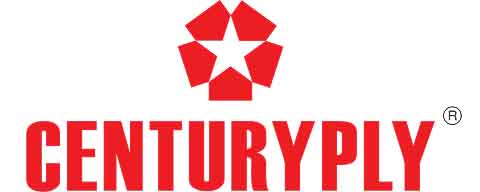
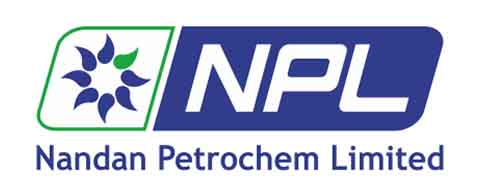
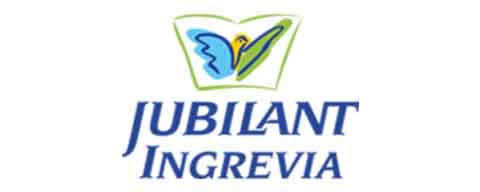
Challenges with other TMS
Lacks expertise
Typical TMS solutions lack deep logistics expertise & fail to adapt to your unique & industry-specific workflows—leaving you stuck with rigid systems that don’t work for your business
Partial coverage, full chaos
Most TMS platforms only handle bits & pieces of your logistics, forcing you to juggle multiple vendors & tools for different processes & modes
Costly & tedious implementation
Endless configurations, broken go-lives & months of waiting—most TMS projects fail before they even take off. And to top it, they don't give you the ROI you deserve!
Fretron fixes what other TMS solutions get wrong
Fully customizable + deep expertise
Our MoveAsOne framework & team of logistics veterans ensure a consultative approach & tailor-fit our TMS to your exact needs!
Truly comprehensive
TMS, FMS, Billing- manage all your processes on our unified platform. We're fully multi-modal covering road, rail, ocean & air seamlessly, & integrate with your ERP to give you the 360 coverage you need!
Fast ROI, seamless go live in weeks!
Realize ROI quickly with a seamless, guided rollout delivering 100% implementation success and high-touch support.
Industry’s Most
Comprehensive TMS Platform
Every process. Every leg. Every mode. Every shipment. Every stakeholder. All on one unified platform!
Fretron simplifies your entire logistics universe—on a single platform.
Better vehicle utilization
Minimize incidental costs
Reduce empty backhauls
Reduce wastage in handling
Reduce weight discrepancies
Reduce manpower costs
Improve vehicle TATs
Better billing reconciliations
Reduce pilferage
& more...
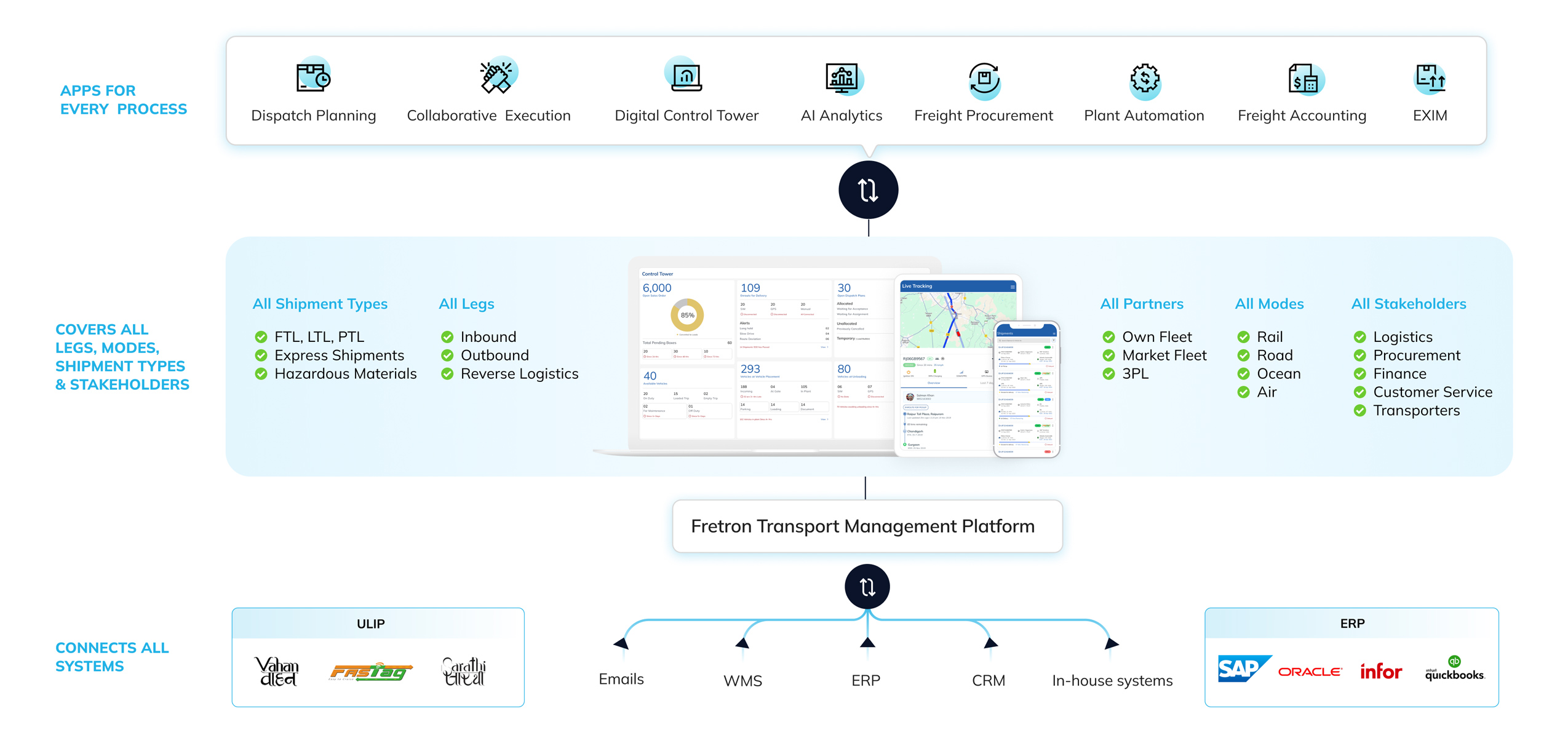
Customized for your industry
Fretron adapts to your business—not the other way around.
Using our domain expertise and the MoveAsOne framework, we tailor the platform to your unique logistics processes.
Better vehicle utilization
Minimize incidental costs
Reduce empty backhauls
Reduce wastage in handling
Reduce weight discrepancies
Reduce manpower costs
Improve vehicle TATs
Better billing reconciliations
Reduce pilferage
& more...
Seamless onboarding in 6 weeks!
Unlock value at speed.
- Expert-led workshops to map your logistics workflows
- Pre-configured best practices to accelerate go-live
- Interactive admin training and live Q&A support
- Continuous alignment with KPIs & business goals
Our team guides you every step of the way ensuring smooth adoption, workflow alignment & measurable success!
Apps for Every Logistics Need.
All in One Platform!
Fast-track ROI realization
Reduction in Yard In-to-Plant Out TAT
On-time deliveries
ePOD enablement
Reduction in manual efforts
Customer testimonials
"Fretron has saved us around Rs. 3 Crore by providing 100% tracking & significant reduction in detention claim & late delivery costs."
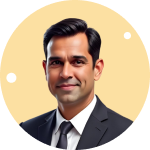
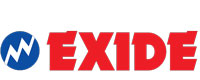
"Fretron’s our go-to TMS tech solution. It’s reduced SKU-level delivery discrepancies and increased shipment visibility. It has greatly improved our on-time dispatches with the load-builder (90% quicker order management). Highly recommended team and product to work with!"
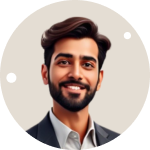
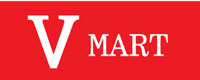
"Fretron's solutions have streamlined our logistics processes, significantly enhancing efficiency & reducing delays. The automation & real-time visibility have transformed our operations & greatly improved customer satisfaction!"
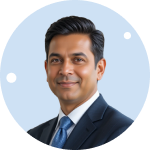
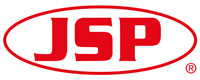
Industries we serve
We enable logistics teams to #MoveAsOne
We bring your teams together to unlock trust, collaboration and efficiency, leading to cost savings and customer delight!
Our credentials
INR handled in freight costs
Shipments handled every year
INR Saved in freight costs
Bring your logistics teams together with our collaborative TMS
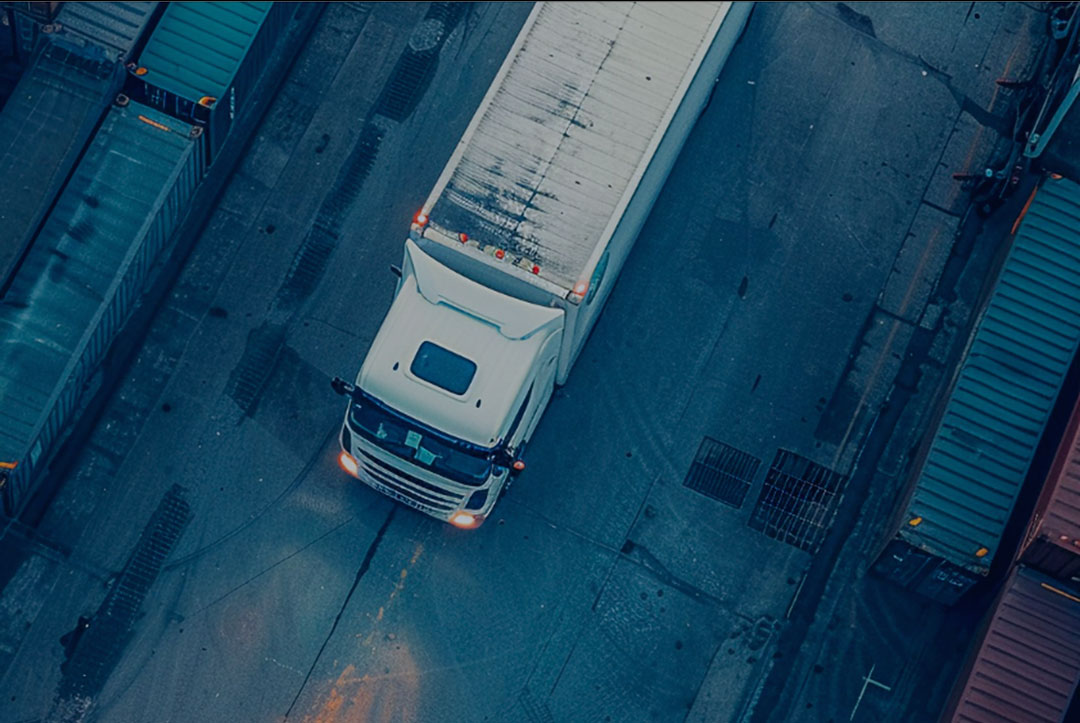
FAQs
Find answers to your most pressing questions about our services and solutions.
Fretron is a collaborative TMS (Transportation Management System) that helps streamline logistics operations. It enables cost optimization, revenue growth, customer satisfaction, digital transformation and compliance in your logistics processes, from freight procurement to load and route planning, dispatch execution, tracking to freight billing and analytics.
Fretron TMS integrates various logistics functions, including planning, execution, and tracking. We provide real-time data and analytics to optimize load, routes, mode selection and reduce delays. This ensures timely delivery and enhances customer satisfaction. Operational efficiency and automation helps make freight cost savings.
Using a TMS can lead to significant cost savings, improved visibility, and enhanced compliance. It streamlines operations and reduces manual errors. Additionally, it helps companies adapt to changing regulations in the chemical industry.
Our pricing varies based on the specific services and solutions you choose. We offer customized packages to fit your business needs. Contact us for a detailed quote tailored to your requirements.
Getting started is easy! Simply reach out to our team for a consultation through our contact us page.