The relentless demand for supply chain agility and efficiency casts a spotlight on the critical shortcomings of manual plant logistics operations. Outdated methods, paper-based inventory, and poor visibility cause delays, errors, and cost increases. These issues make it hard to meet demands for quick, accurate deliveries, putting companies at a competitive disadvantage. This is the "mayhem" of manual plant logistics.
This often results in limited visibility into inventory levels, material flow, and equipment performance. Delays and errors become commonplace, leading to dissatisfied customers and lost business opportunities. Employee fatigue and high turnover rates become noticeable. Whether it's fluctuating order volumes or new product lines, manual processes can't keep up with changing demands. And then, data silos and limited transparency make it impossible to identify bottlenecks, optimize resource allocation, or make proactive improvements.
The urgent need for optimization is clear – to survive and thrive. It's time to ditch the chaos of manual processes and embrace a future of efficient, cost-effective plant operations.
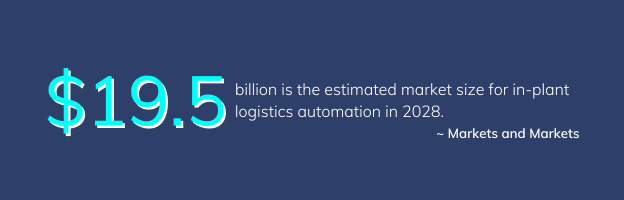
The Limits of Traditional Plant Optimization
Logistics managers are constantly seeking ways to optimize plant operations, but traditional methods often fall short in addressing today's complexities.
- Manual and ERP-based Monitoring
Manual inspections with data entry into Enterprise Resource Planning (ERP) systems offer a degree of control but result in processing delays, poor dock scheduling, and increased turnaround times for shipments.
Hectic Paperwork, involving time-consuming vehicle inspections, documentation, and safety protocol checks, often leads to errors and compliance violations. Limited Visibility of ERP systems disables real-time insights into congestion points and their causes. Static Processes with inflexible, pre-defined routes fail to adapt to changes in material flow, creating additional inefficiencies.
- Non-Standardized Workflows
Reliance on manual, unstandardized processes introduces significant inefficiencies, generating bottlenecks and inefficiencies, increasing TATs, and reducing plant productivity.
Conventional plant logistics optimization suffers from Inconsistent Inspections involving varying procedures leading to delays and data inconsistencies. Unoptimized Loading/Unloading lacking standard protocols increases handling times.
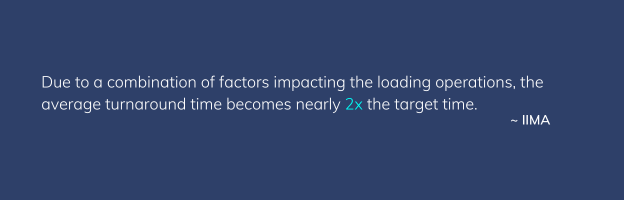
- Spreadsheet-based Yard Management
Yard management often depends on spreadsheets to monitor KPIs, leading to inefficient use of resources and operational delays.
Data Inaccuracy resulting from manual data entry errors compromises KPI reliability and decision-making. Limited Insights are marked by an inability to analyze trends or pinpoint improvement areas. Lack of Scalability with growing operational volumes hamper efficient resource allocation.
Stepping into the Future: Technological Solutions for Plant Optimization
While traditional methods have their place, the complexities of modern logistics demand a more advanced approach. Plant heads and logistics managers are increasingly turning to technology to overcome limitations and optimize their operations.
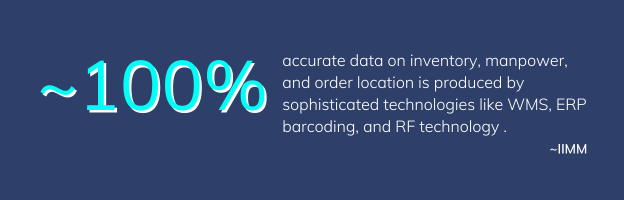
- Warehouse Management Systems (WMS)
These software platforms manage inventory levels, track materials, optimize picking and packing processes, and provide real-time data insights. WMS can significantly streamline workflows, reduce errors, and facilitate better resource allocation.
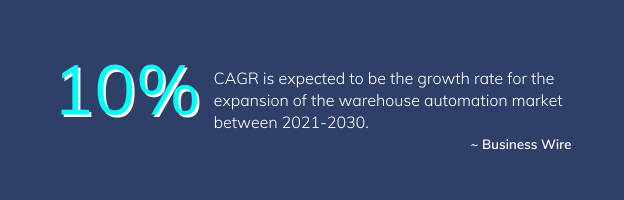
- Yard Management Systems (YMS)
These specialized systems streamline yard operations by managing truck scheduling, dock appointments, and yard movement. YMS solutions improve space utilization, reduce congestion, and optimize truck turnaround times.
- Automated Storage and Retrieval Systems (AS/RS)
These robotic systems automate the storage and retrieval of materials within the plant. AS/RS can significantly increase storage density, reduce picking times, and minimize human error.
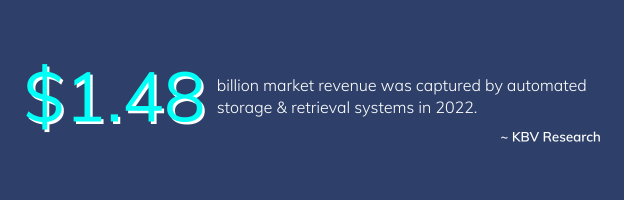
- Real-Time Location Systems (RTLS)
These systems use technology like RFID tags or Wi-Fi to track the real-time location and movement of assets, materials, and vehicles, enabling proactive management of congestion and bottlenecks.
- Autonomous Mobile Robots (AMRs)
These self-driving robots can automate tasks like transporting goods between production lines, picking and placing items in storage, and moving materials to shipping docks. They offer greater flexibility and scalability.
- Integration Platforms
These platforms connect various software applications and devices within a plant environment, ensuring seamless data flow and eliminating data silos, enabling a unified view of plant operations ultimately.
- Transportation Management Systems (TMS)
Playing a pivotal role in end-to-end plant logistics automation, TMS streamlines operations through digitalized tracking, standardized workflows, and real-time data analytics. This integration enhances visibility, improves accuracy, and facilitates scalable logistics solutions, ensuring operational efficiency and adaptability to dynamic market demands.
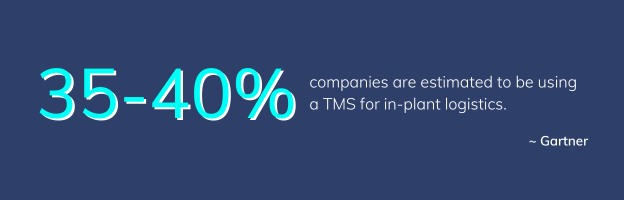
Existing Tech Solutions: Stepping Stones, Not the Finish Line
While these technological advancements are powerful tools, they still have limitations that prevent them from offering a complete solution:
- Cost and Implementation
Some solutions, like AGVs and advanced data analytics platforms, require significant upfront investment and technical expertise to implement. This can be a barrier for smaller businesses.
- Integration Challenges
Integrating disparate systems can be complex and costly. Data silos may persist if integrations are not seamless, hindering the flow of information and overall visibility.
- Data Quality Dependence
The effectiveness of data-driven solutions relies heavily on the quality and accuracy of data input. Poor data quality leads to misleading insights and hinders effective optimization.
- Limited Scope
Many solutions address specific areas like warehouse management or yard operations. A truly comprehensive approach requires a holistic solution that integrates all aspects of plant logistics seamlessly.
These limitations highlight the need for a more unified approach to plant optimization.
The Future of Plant Logistics is Fully Automated
The limitations of traditional methods and existing tech solutions pave the way for a more powerful approach: End-To-End Automation.
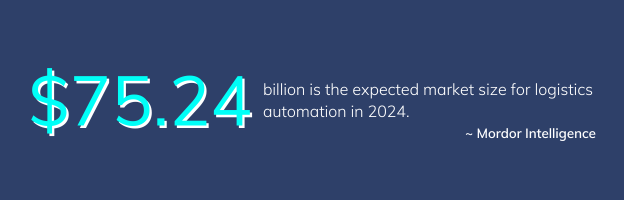
Imagine a plant where machines handle tasks efficiently, real-time data guides decision-making, and operations adapt effortlessly to changing demands. This is the future that automation promises.
Automation injects intelligence and precision into plant logistics. It streamlines operations by automating repetitive tasks, freeing up human resources for higher-level functions. Real-time data from automated systems provides complete transparency, allowing for proactive decision-making and improved control. Additionally, automation offers unmatched scalability and adaptability – a perfect fit for today's dynamic market demands.
Plant logistics automation brings a powerful combination of benefits to the table.
- Streamlined Vehicle Processing
Automation eliminates human error and delays in vehicle registration and inspection through automated digital workflows, significantly reducing vehicle turnaround times for efficient and accurate processing.
- Enhanced Operational Visibility
Real-time monitoring with stage-wise analytics overcomes manual tracking limitations, providing clear insights into operational bottlenecks. This enables process optimization for faster dispatch and improved efficiency.
- Accurate Load Management
Direct system integration with weighing equipment automates weight capture, minimizing manual intervention. This ensures load compliance and dispatch efficiency by eliminating inaccuracies and speeding up the process.
- Optimized Loading Operations
Digital management of loading bay operations replaces inefficient paper-based systems, optimizing loading procedures. This reduces vehicle waiting times and ensures timely dispatch, enhancing throughput.
- Automated Documentation and Compliance
Automation in generating invoices, waybills, and PGI/GRN documents streamlines documentation, improving accuracy and compliance. This accelerates billing cycles and enhances customer satisfaction.
- Data-Driven Strategic Insights
A shift to data-driven analytics dashboards offers real-time operational reporting and insights. This empowers plant logistics teams with actionable intelligence for continuous improvement and strategic decision-making.
The TMS Blueprint for Plant Logistics Automation
Harnessing the power of a Transportation Management System (TMS) transforms plant logistics from a challenge into a strategic asset.
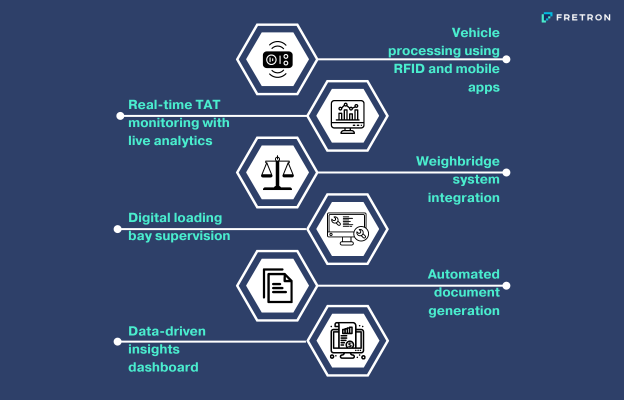
- Digital Workflows for Vehicle Processing: Automated vehicle registration and inspection with RFID tagging and mobile app support streamline entry and exit processes.
- Real-Time TAT Monitoring: Live dashboard analytics for stage-wise turnaround times, enabling quick identification and optimization of operational bottlenecks.
- Weighbridge System Integration: Direct integration facilitates automatic capture of tare and gross weight, ensuring accurate and efficient load management.
- Digital Loading Bay Supervision: A comprehensive digital portal for real-time loading bay status, vehicle allocation, and dispatch scheduling optimizes loading operations.
- Automated Document Generation: Instant creation of invoices, waybills, and PGI/GRN documents integrated with logistics operations enhances compliance and customer satisfaction.
- Data-Driven Insights Dashboard: Real-time reporting and analytics on logistics performance, offering actionable insights for strategic decision-making and continuous improvement.
By automating intricate logistics operations, TMS brings unparalleled efficiency, accuracy, and insight to the forefront.
Connect with us to know the best strategies and how you can leverage powerful Fretron TMS' capabilities to revolutionize the way your plant operates. You can alternatively email us at sales@fretron.com or call us at +91 9711799111.